部品の軽量化で
こんなお困りはありませんか?
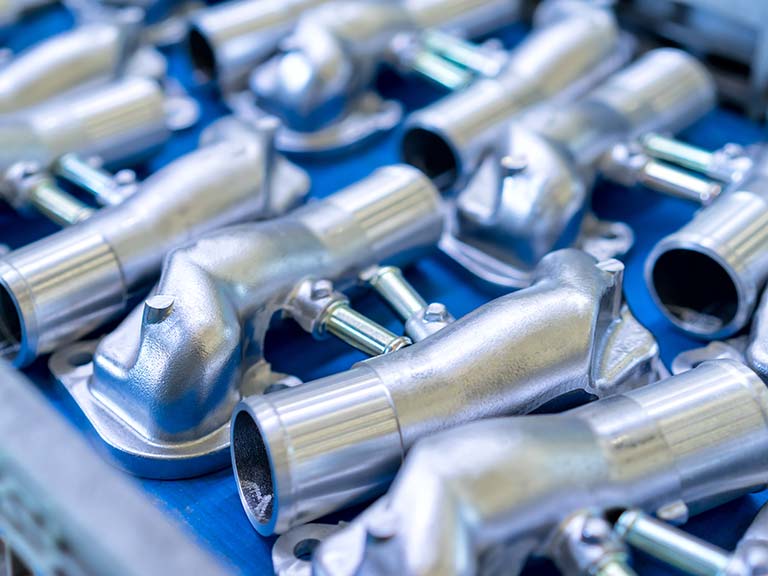
鉄からアルミへ置き換えて、部品を軽量化したい
鉄にくらべ、1/3の軽さを誇るアルミ合金
アルミによる部品の軽量化のニーズは増加していますが、一方で強度とコストの問題から、その置き換えは進んでいません
一般的なアルミ鍛造のデメリット
- 強度が低い
- 強度が鉄の半分程度
- コストが高い
- 鉄にくらべ材料費・工数がかかる
部品の軽量化を
高強度アルミ鍛造が解決!
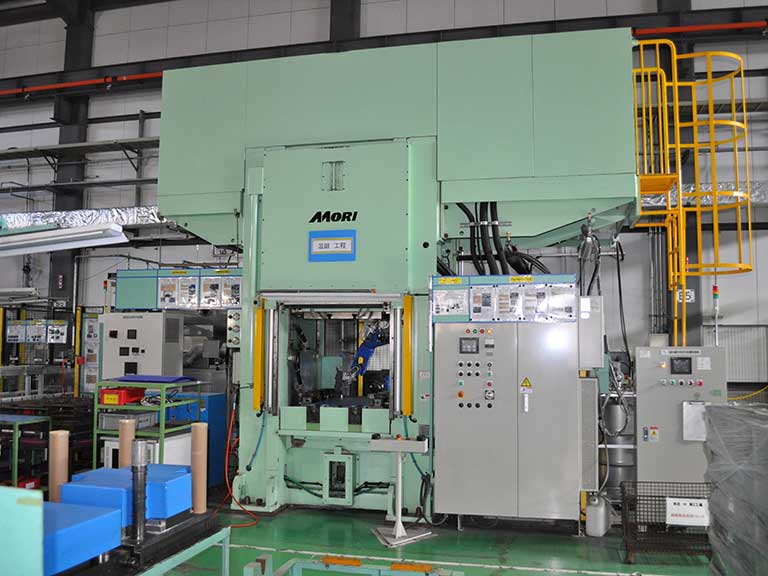
戸畑ターレットでは、アルミ合金の強度向上を実現する「高強度アルミ鍛造」工法を開発
既存の冷間鍛造によるアルミ鍛造品にくらべ、鉄並み高強度・低コストのアルミ鍛造を実現
自動車部品をはじめ、さまざまな産業部品の軽量化・強度向上に貢献しています
高強度アルミ鍛造の事例
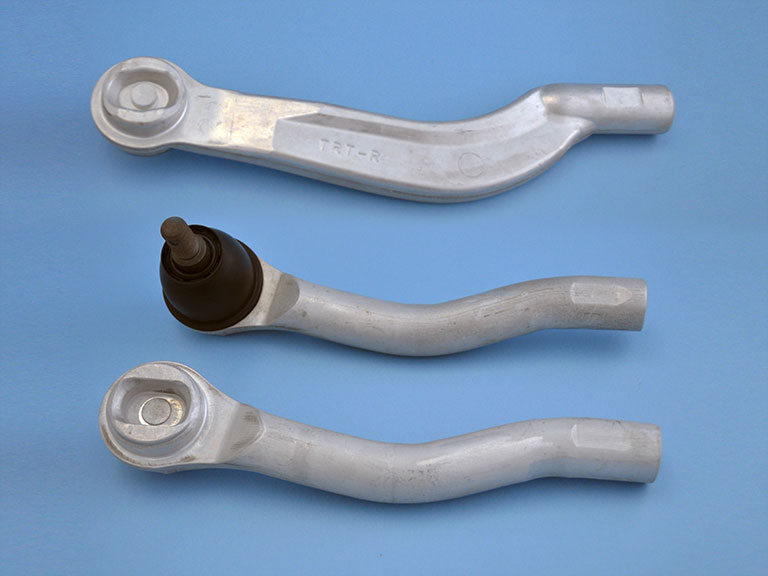
アルミの「軽さ」を活かした製品開発が実現します
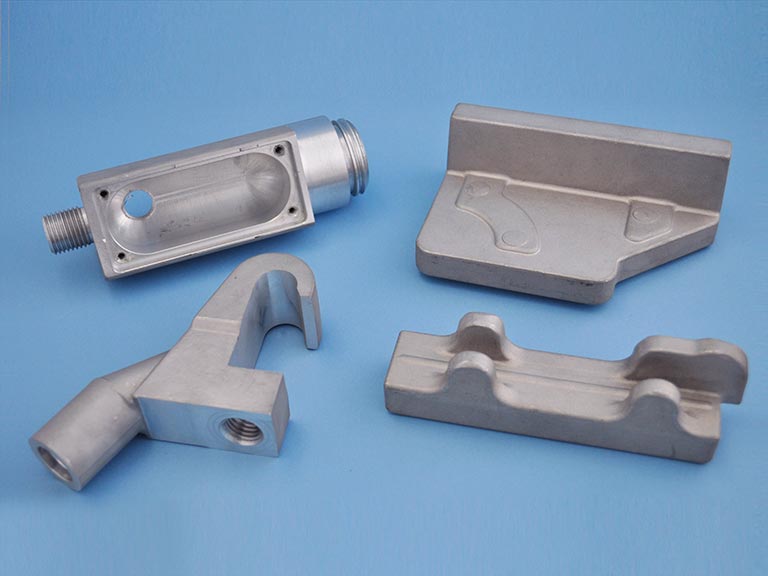
繰返し衝撃に耐える高強度な部品製造が実現します
高強度アルミ鍛造のメリット
- 強度向上
- 鉄に対して、約81%まで強度が向上
- 大幅な軽量化
- 鉄からの置き換えで、1/3の大幅な軽量化を実現
- コストメリット
- 鉄の鍛造品と遜色のないコストで、量産が実現
既存の鍛造技術との比較
比重の比較
鉄にくらべ比重が1/3と軽量
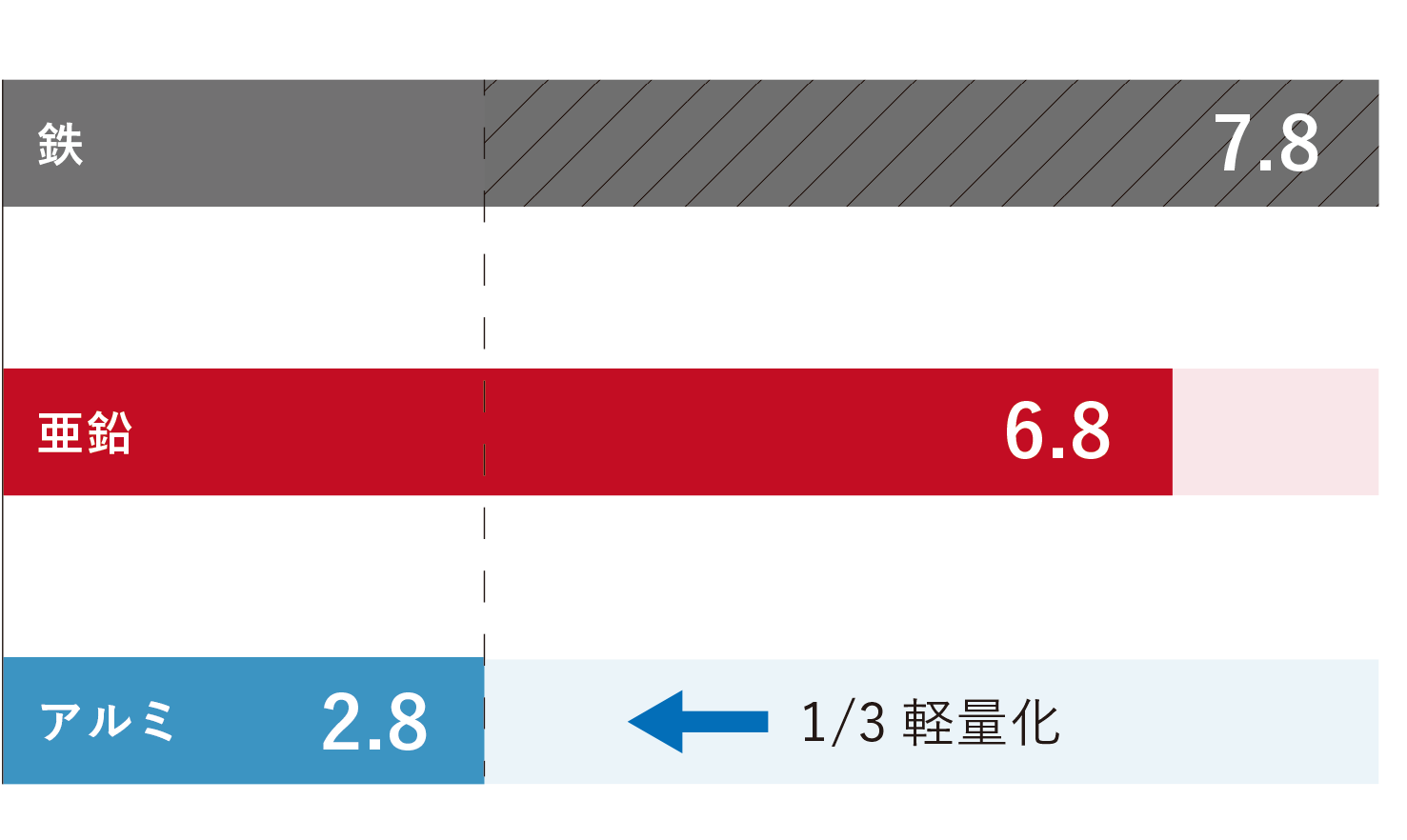
強度の比較
アルミ冷間鍛造とくらべ、強度が1.6倍に向上
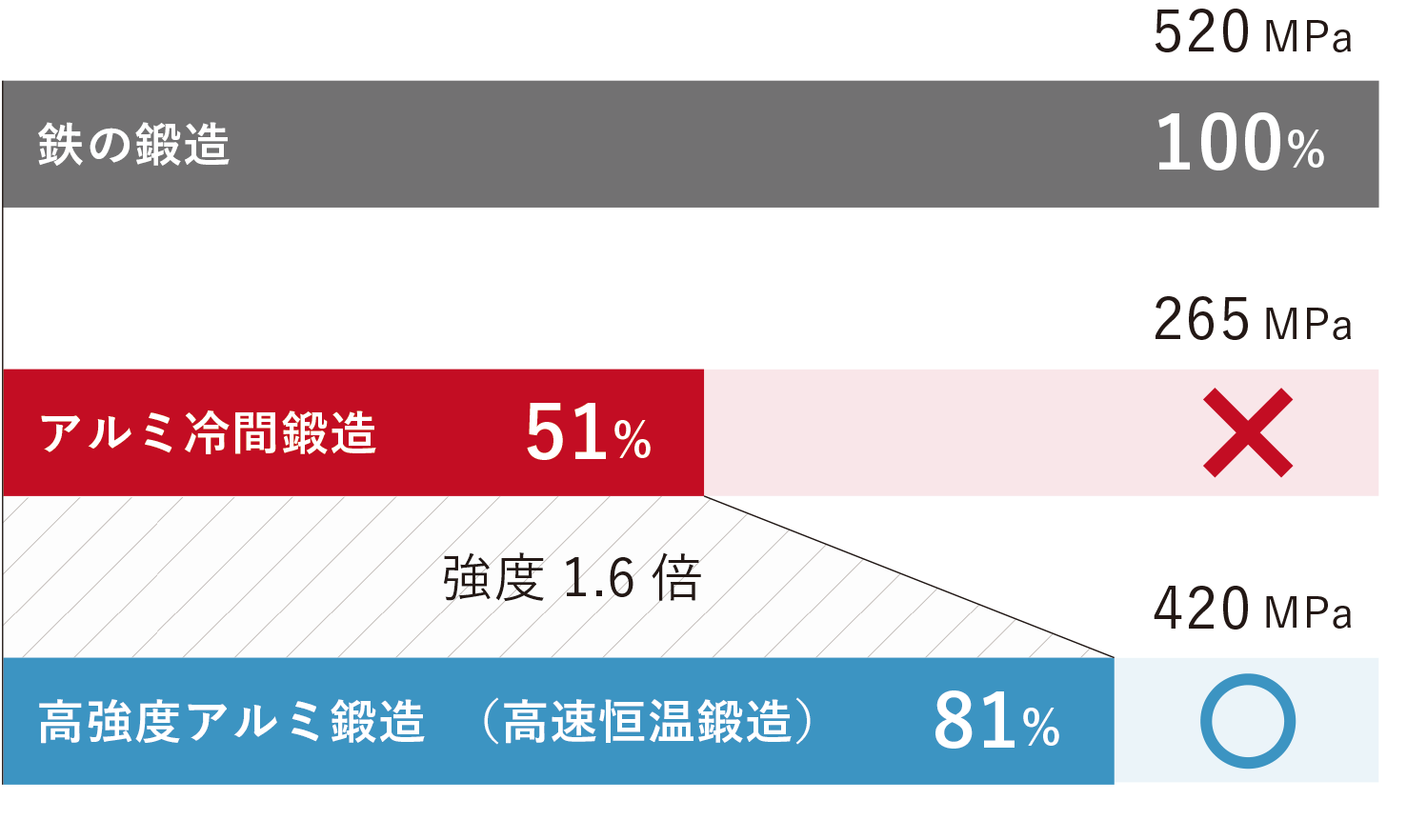
鉄の鍛造との比較
工法 | 鉄の鍛造 | アルミ冷間鍛造 | 高強度アルミ鍛造 | ||
---|---|---|---|---|---|
項目 | 鍛造+焼きならし (材質:炭素鋼S35C) |
冷間鍛造+T6処理 (材質:A6061) |
温間鍛造+T6処理 (材質:A6061) |
高速恒温鍛造 (材質:A6061) |
|
特徴 | 一般的な鉄の鍛造工法 | 一般的なアルミ鍛造工法 強度が低く、鉄からの置き換えはできません |
当社独自のアルミ鍛造工法 一般的なアルミ鍛造とくらべ、大幅に強度が向上します |
当社独自のアルミ鍛造工法 当社のアルミ鍛造のなかでも、最も強度が高い工法です (詳細はこちら) |
|
引張強さ | 520MPa | 265MPa | 360MPa | 420MPa | |
耐力 | 320MPa(降伏点) | 245MPa | 340MPa | 400MPa | |
伸び | 23% | 10% | 18% | 14% | |
硬さ | 155HV | 90HV | 135HV | 145HV | |
工程数 | 3 | 5 | 4 | 4 | |
造性 | 良 | 難形状不可 | 最良 | 良 | |
コスト比較※ | 10 | 15 | 12 | 11 |
※鉄を10とした時の比較
金属組織の比較
TEM(透過電子顕微鏡)観察による、一般的なアルミ鍛造との比較
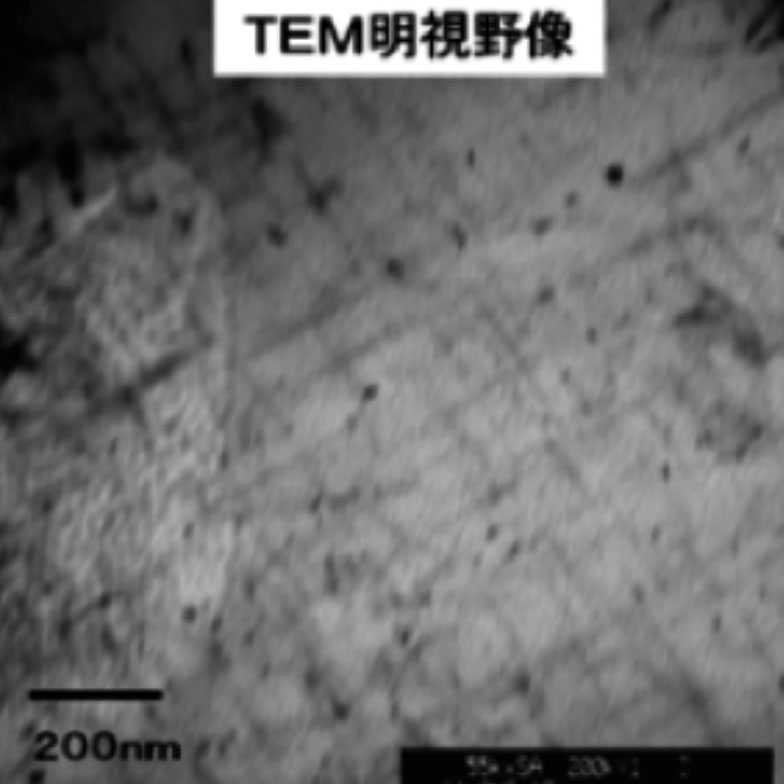
一般的なアルミ鍛造(冷間鍛造+T6処理)
析出物である針状のマグネシウムシリケイト(Mg2Si)がみられます
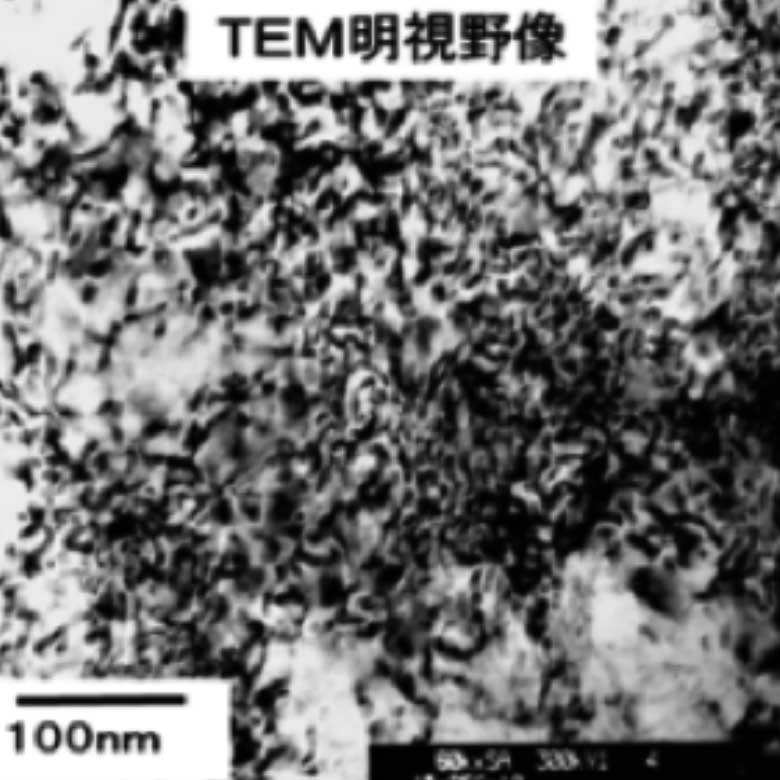
高強度アルミ鍛造(高速恒温鍛造)
微細再結晶粒・転位・析出物の集積した複合組織
金属組織にひずみが残り、強度が得られます
採用事例
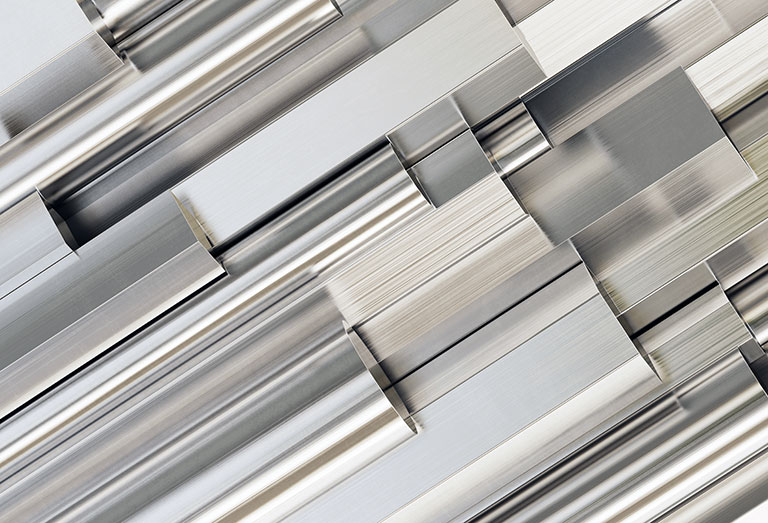
アルミ鍛造品の用途
アルミ合金は、耐食性・加工性に優れた非鉄金属です。
高強度アルミ鍛造によりさらに強度を高めることで、部品の軽量化・肉薄化が実現。
リサイクル性も高いため、省エネやCO2排出削減の観点からも、あらためて注目されています。
一般的なアプリケーション
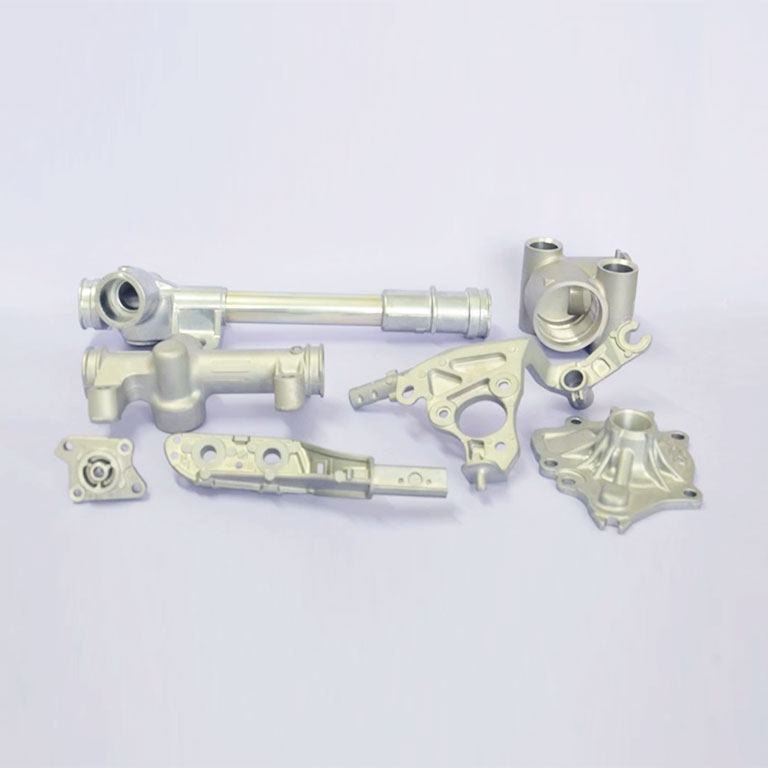
- 自動車部品(エンジン/ステアリング/ハウジングなど)
- 航空機部品
- エレクトロニクス関連部品
- 油圧/空圧機器
- ブラケット/機械要素部品
- その他産業機械 など
戸畑ターレットの
高強度アルミ鍛造が選ばれる理由
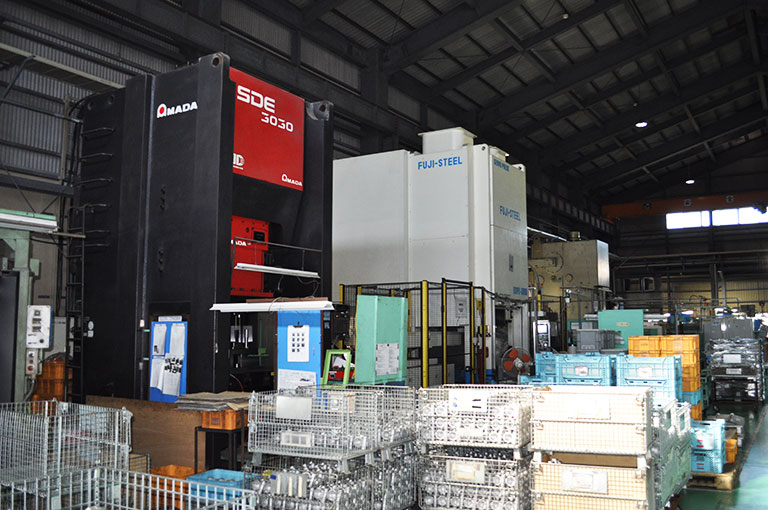
非鉄金属加工のエキスパート企業
1962年の創業以来「非鉄のエキスパート」として、北九州から全国へかけ多くのものづくり企業の課題を解決。
大手自動車部品メーカーをはじめ、産業機械や設備メーカーなど、500社以上の取引実績があります。
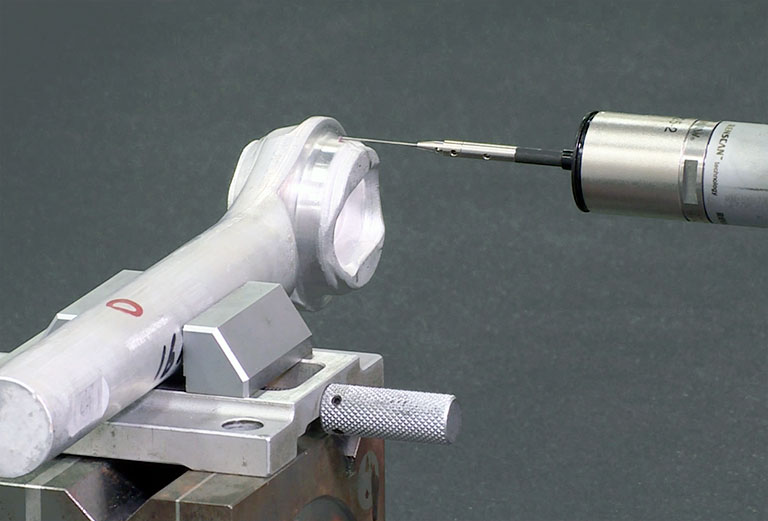
「ものづくり日本大賞 優秀賞」受賞
高強度アルミ鍛造は、北九州の産学官が連携し開発に取り組んだ、業界初のアルミ高強度化鍛造技術です。
(九州工業大学との共同研究により特許を取得)
2018年には、経済産業省「ものづくり日本大賞 優秀賞(製品・技術開発部門)」を受賞し、公的機関からも高い評価を得ています。
高強度アルミ鍛造技術の賞歴・認定
- 2007年
- 中小企業庁「経営革新計画」
テーマ:自動車軽量化に資するアルミ鍛造品製造 - 2008年
- 経済産業省「戦略的基盤技術高度化支援事業(サポイン)」
テーマ:自動車部材向けアルミニウム合金高速恒温鍛造技術の開発 - 2014年
- 経済産業省「戦略的基盤技術高度化支援事業(サポイン)」(2回目)
- 2018年
-
経済産業省「ものづくり日本大賞 優秀賞」製品・技術開発部門
テーマ:自動車用鉄部品をアルミへ置換することを可能とするアルミ高強度化鍛造技術の開発
鍛造の関連ページ
機械部品の軽量化、
鉄からアルミへの置き換えを
ご検討の方へ今すぐ!お問い合わせください
試作から量産まで、経験豊かなエンジニアが直接ご相談に応じます。
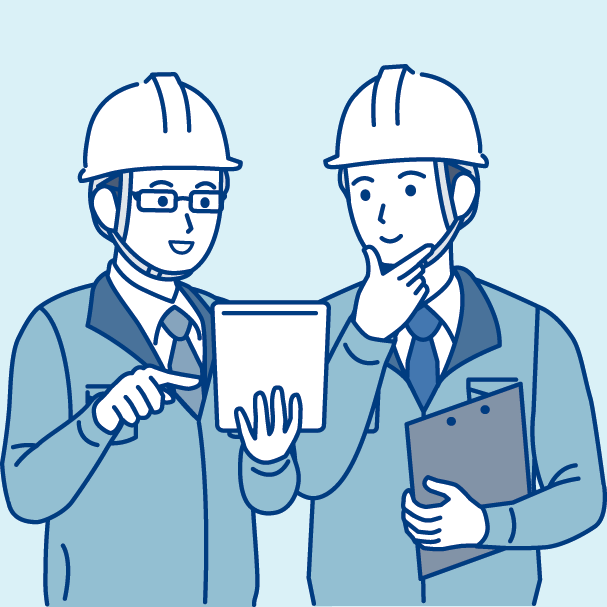
そのため製品化にあたっては金型設計から試作・耐久評価まで、お客様と連携して行う必要があります。
詳しくはお問い合わせください。
-
開発・製品化の流れ
(クリックで表示)1お問い合わせ
ご相談内容をご自由にご記入ください。
鍛造へ切り替えたい既存製品の図面をお送りいただいても構いません。2ご提案・お見積もり
専任の担当者がお客さまのご要望をヒアリング。
ダイカストイからの置き換えや切削品の鍛造化など、最適な工法をご提案いたします。3試作品の鍛造
鍛造図面をもとに金型設計。
試作用プレス機を使い、試作品を鍛造します。4量産スタート
試作品をもとに最終調整を行い、量産を開始。
鍛造後の機械加工や表面処理など、二次加工にも対応いたします。
直近のご相談例
- 鉄からアルミ鍛造へ切り替えて、部品を軽量化したい
- アルミ部品の強度を上げて、肉薄化したい
- 自動車向けアルミ鍛造品は、製造コストが高い?
- 切削品を鍛造化して、トータルコストを削減したい
- 鍛造後の二次加工も一貫して依頼したい
お問い合わせ窓口
◎受付時間 平日 9:00~17:00
(土曜・日曜・祝日・年末年始を除く)
非鉄鍛造についてお気軽にご相談ください
高強度アルミ鍛造から銅・真鍮鍛造まで、
経験豊かなエンジニアが直接ご相談に応じます